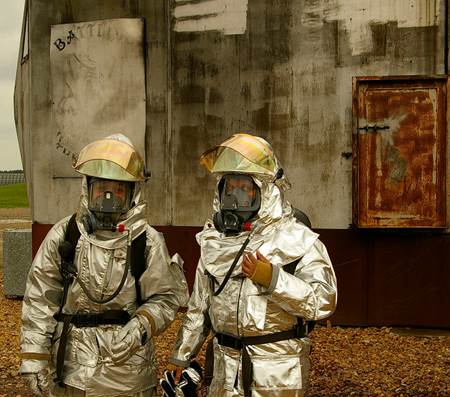
The fire service has been inundated with specific issues related to cancer-causing substances and practices for avoiding exposure to carcinogens and other harmful substances.
This subject has taken several different directions, one of which is to look at the PPE itself as a potential source of chemicals that, over time, get into the firefighter’s body and contribute to long-term health problems.
It has been our opinion that the real dangers of fireground exposure occur as a result of:
- Having contact with different substances through respiration (not wearing the SCBA all the time it is needed)
- Skin contact during emergency itself (problematic when dirty clothing is not removed after use or when showers are not taken after the fire event)
- The continued exposure to persistent contaminants that remain in unclean PPE (when firefighter clothing is not cleaned after fireground exposures)
Nevertheless, allegations have been made with respect to certain substances leaching out from clothing components, evaporating from the clothing during use, or otherwise causing firefighter exposure.
Understanding PPE as a chemical exposure threat is murky. While certain substances may or may not be present in turnout clothing, the extent to which they are present and more importantly, the manner in which they may present themselves as a hazard for exposure has not been fully determined.
To date, there have not been any studies that definitively show the quantity of particular substances that comes out of the turnout clothing and gets into firefighters’ bodies by any route of exposure. This does not mean to say that this does not happen – the topic simply has not been studied adequately.
This should not further imply that industry should just wait for all the research to be done just because specific risks have not yet been quantified. Instead, industry should move forward with actions that minimize the potential risks to fire fighters who already operate an ultra-hazardous environments.
EXISTING AND EMERGING REGULATIONS AND THEIR IMPACT
Large parts of the consumer textile and other industries are already addressing potentially hazardous substances that may be used in very small amounts as part of their products through what are called restricted substances lists (RSLs). These are lists of compounds with known adverse health effects that have either been banned or are being closely scrutinized by different jurisdictions whether by regions, countries, states or even cities.
RSLs include a variety of chemicals, such as plasticizers, certain toxic heavy metals, different dyes and other substances that have been discovered to pose particular toxic or carcinogenic effects. Most often, the chemicals on RSLs are subject to certain limits, but these can vary from jurisdiction to jurisdiction.
California Proposition 65 is an example of an RSL that is well-established in the United States. Its main intent is to protect drinking water from contamination by hazardous substances. The list now contains over 800 naturally occurring and synthetic chemicals that are known to cause cancer, birth defects or other forms of reproductive harm. They include additives or ingredients in pesticides, common household products, food, drugs, dyes or solvents. They can also be chemicals used in manufacturing and construction, or byproducts of chemical processes, such as motor vehicle exhaust.
The state regulations establish safe harbor levels for some of these chemicals in terms of a known concentration that does not cause harm or in the form of allowable daily dose. The regulations do not prescribe safe levels for products, but do require manufacturers of products that contain these substances to provide a warning that Proposition 65 substances are present.
A more recent example specific to the fire service and certain chemicals occurred when the State of Washington enacted new state regulations in July 2018 banning the use of Class B firefighting foams that contain perfluoroalkyl substances (PFAs), with certain exceptions. It further required manufacturers of firefighter PPE which contain any PFAs to disclose that information to the departments who purchase the PPE and to indicate the reasons for why PFAs are used in the product. This is a particularly aggressive regulation because PFAs are a very broad class of chemicals for which only a few chemicals are known to have any toxicological properties. According to an FAQ published by the Environmental Protection Agency (“EPA”), PFAS are present in a variety of common consumer goods, such as food packaging, cookware, cleaners, etc.
The fire service PPE industry reacts to these regulations in the respective areas where they apply but the reality is that these requirements do not uniformly pertain to the U.S. fire service. Regulations affecting California or Washington are not addressed elsewhere. Moreover, some areas of the country are in the process of setting different restrictions for specific substances that may vary dramatically. While the intent of these regulations is laudable, the fire service is not gaining the overall benefit. Consequently, industry needs to get ahead of this problem by working with standards organizations to create consistent requirements.
A POSSIBLE SOLUTION FOR FIREFIGHTER PPE MANUFACTURERS
Instead of PPE manufacturers attempting to maintain their own RSLs that cobble requirements of different states or local areas, and deciding when and where to disclose or control constituent parts of their products, a better approach would be to adopt a universally recognized set of criteria that can be applied to the entire industry. There is already comprehensive knowledge on restricted substances in textile and related products but there are no specific requirements for testing and no uniform set of criteria for potentially hazardous components that are determined independently.
Fortunately, there are organizations that exist which offer these services, and which have been in use primarily in the consumer field for indicating that products including the fabrics and other components are either free of or have the lowest safe levels of pertinent restricted substances.
One such organization has created the Oeko-Tex Standard, which is an independent certification system testing textiles for “harmful substances.” When a textile is certified to the Oeko-Tex Standard, it means that it has met certain criteria:
- It contains no illegal substances (carcinogenic colorants).
- It only has a certain amount of other legally regulated substances (e/g/, formaldehyde, heavy metals, phthalates, etc.).
- It only contains a certain amount of substances that are known to be harmful but are not yet regulated at all (e.g., pesticides and allergenic dyes).
The Oeko-Tex Standard is far more strict than legislation in the U.S., and the amounts of these chemicals allowed in certain products depends on the article’s use. There are four product classes, each of which has its own limits for various substances.
Moreover, there is a specific variant of this standard that addresses protective clothing. While the standard originated in Europe, it has been adopted through various well known product outlets, manufacturers and suppliers in the U.S., including some components providers of turnout clothing. The adoption of this or similar practices within the fire service PPE industry would seem to provide broad benefits to the fire service.
NFPA RECOMMENDATIONS
It is our recommendation that NFPA PPE product standards consider incorporating systematic ways of regulating restricted substances for new products. By adopting new requirements as part of NFPA involving independent testing and certification of PPE for restricted substances, concerns over one path of potential exposure can be eliminated.
This approach is no different than what is already done for establishing acceptable levels of protective performance by third-party certification. Requirements for restricted substances must be further coupled with investigations of the real hazards from legacy gear so that the science can used to establish if any risks exist. Only in this fashion can confidence be established for the fire service in addressing overall chemical exposure safety.
—
The views of the author do not necessarily reflect those of the sponsor.