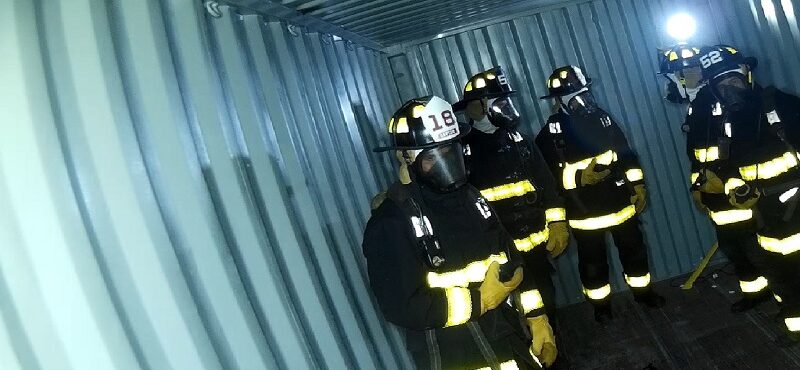
By Edward McCarthy, Logistics Manager, Boston Fire Department
The Boston Fire Department (BFD) has a long and proud history, one that we take great pride in. Boston has been at the forefront of the fire industry for well over 300 years. It was the first fire department in North America, tracing its lineage back to 1678. In 1851, the BFD was the first department in the world to protect the city through the use of a public telegraph fire alarm system, a system still in operation today. The BFD operated the first fire engine, a hand engine, put into service in 1678. It was one of the first to purchase a steam engine, one of the first with a fire boat, one of the first to use radio for communication. We pushed for, helped develop, and were the first department in the country to use modern breathing apparatus. While we are proud of our past, we must also be focused on the future, and we must always strive to continually improve.
The Cancer Threat
Recently the fire service, and Boston in particular, has been struggling with the reality of an ever-increasing number of firefighters being affected by cancer. While the reasons for this are hotly debated, the effect has been devastating. In Boston, 1 in 6 members will develop cancer and some will never recover. We have taken many steps to reduce exposure to toxic substances, increased physical fitness programs, shown members the benefits of healthy diets, and created a host of post incident decontamination processes. However, we felt that there was more that could be done. One area which we wanted to explore was bunker gear. We wanted to know how well bunker gear actually protected members from particulates and what, if anything, could be done to improve it. This led us to start a dialog with several bunker gear manufacturers.
In our meetings and discussions, we looked at different ways to limit particulates from contacting the wearer. What we found out initially is that bunker gear does a tremendous job of blocking harmful particulate matter; however, it has an Achilles heel – interfaces. Most bunker gear is two pieces – jacket and pants. The jacket overlaps the pants; the pants overlap the boots; the gloves overlap the jacket; and the hood is tucked in to the collar. What we wanted to know was how well it protected the wearer from particulates. We also wanted to test some ideas we had to improve it. One idea had come from Globe. The idea was basically to add an environmental barrier into the garment around the interfaces. Globe believed that by adding this barrier they could significantly reduce the amount of particulate entering the garment while not substantially adding to heat stress on the firefighter. Globe agreed to engineer and manufacture the garment; we just needed to figure out a way to test it.
Test Methodology
The testing would need to test two basic things. First we had to determine if the garment would be more effective than our current gear in stopping particulate matter. Secondly, we wanted to see if the gear would add to the physiological stress of the firefighter wearing it.
The first test needed to simulate the size of particulates found in a typical fire. It had to be safe for the members who would be taking part in it. We looked at several studies that had been conducted and their use of a test method called FAST. This is an aerosol test, conducted at a lab. It is highly scientific; however, it also was highly expensive. The testing of a single garment can cost into the tens of thousands of dollars. That put it well outside BFD’s grasp. We needed to find a different method of testing that would approximate the results seen in FAST testing, but at a significantly cheaper cost. Luckily, we had an idea of a test method that may work. Some months earlier, we had created a test to determine the permeability of our hoods.
During this testing we had identified a product called Glo Germ. Glo Germ is the trade name of a product made with melamine resin. It is used most frequently in teaching proper handwashing techniques to children and healthcare workers. It is non-toxic. It also approximates the size of particulate matter found in fires. As importantly, it glows under UV lighting, making contamination visible under black light. It was available in both solution and powder forms. We decided to try both forms.
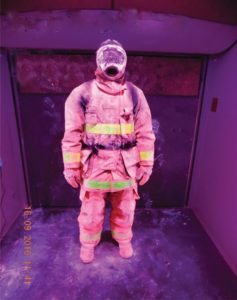
We needed to refine the process of distribution. During the hood testing we had tried several different methods of distributing the product, with mixed results. We first tried to distribute in a solution using a fog machine; however, besides destroying two fog machines, we accomplished little. We then tried dispersing the solution with an airless paint sprayer. This had a more positive outcome; however, it required that we paint the subjects like we were painting a wall. It was therefore ineffective. Finally, we tried it in the powdered form. In these trials we used a fan to disperse the product. This process worked well for dispersing the material; however, we felt it could be improved on for this trial. The answer was pest control. Exterminators frequently need to disperse insecticides in powder form, and to do this, they use a piece of equipment called a duster. The duster is used by exterminators to distribute powdered insecticides in large open areas, such as attics. We felt we had a solution to the distribution problem.
Physiological Monitoring
For the physiological testing process, Globe thankfully had a solution with their Wearable Advanced Sensor Platform system (WASP™). The WASP™ system allows for the collection of a variety of physiological data such as heart rate, respiration rate, and others. It then can take all that information and, through some pretty advanced algorithms, give you a fairly good idea of important metrics such as heat stress, core temperature, and exertion levels. It is also non-invasive, which the participants would be appreciative of.
Particulate Testing
We then had to design the experiments. We decided that we would do two tests over two days, repeating each test each day. We would do a physical fitness test followed by the particulate testing. We decided on using five participants. Three would wear standard issue bunker gear one day and the modified bunker gear on the second. The other two members would wear unmodified gear on both days and would serve as controls. With all of that in place, we were ready to test.
The testing was conducted over two days in September of 2016. Both days the weather was very similar. Temperature, humidity, and other environmental considerations were almost identical.
On day one, each member was given a new set of bunker gear, new helmet, new gloves, new boots, and a new hood. Each participant was checked to ensure the gear fit properly. The participants were first instructed to complete a modified version of our functional skills test while wearing a WASP™ enabled base layer shirt. The test replicates several tasks a firefighter would be expected to conduct on the fireground. For this testing participants scaled a pitched roof, walked along the ridgepole, and then descended. Next the members raised a 35’ ground ladder and fully extended, then retracted, it. Next participants went on air and ascended six stories in our burn building carrying a high rise hose pack. Once they exited the building, they entered an attic prop. Next they were led to the ceiling pulling prop where they conducted ten evolutions of pulling a ceiling. Finally, they entered a short maze section.
After a brief rest, the participants then went into the chamber to begin the particulate testing. In this test, participants were placed in a new 20 TEU shipping container. Once inside the container they went on air and the environment was charged with particulate matter. They then completed a series of simulated fireground activities for approximately 15 minutes. Once time had elapsed, they exited the chamber and proceeded to a trailer that had been modified with UV lighting. Participants were assisted with removal of their bunker gear. Video and photographs were taken throughout this process.
Day two was conducted in the same manner as day one, except three participants were wearing gear that had been modified with the environmental barriers by Globe. All of the gear was new and was not used the previous day. This was to limit the possibility of cross contamination. The participants completed the functional skills test and then proceeded to the particulate testing. The procedures were repeated with photographs and video being taken.
The Results
The results of this testing by the Boston Fire Department showed definitively that by adding the environmental barriers there was significant reduction in the amount of particulate that entered the garment. Further, the Globe WASP™ system revealed that there was no appreciable impact on the physiological health of the participants wearing bunker gear with environmental barriers. The photo below from the study illustrates the results.
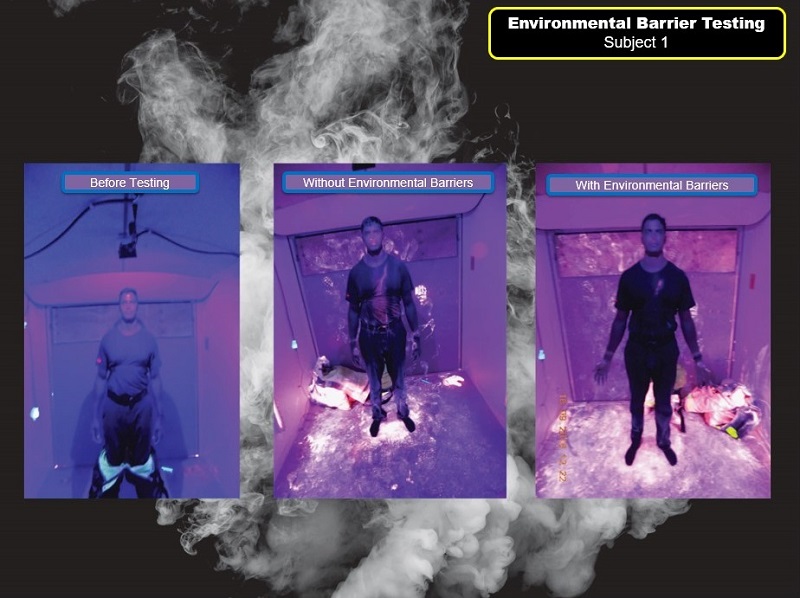